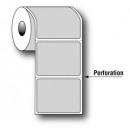
Perforation of the labels are symmetrical holes, placed linearly, typically used to facilitate the detachment of each part of the label material. Perforation is a method of self-adhesive labels for easy separation of the silicone base is separated. Characteristic cut labels - perforated, is also used in non-adhesive labels in which the material is distributed properly. Perforation depends on the shape of the punch notch label. The perforations may be of various types, can more or less to facilitate peel material.
Perforations labels are made to individual order.
Most dimensions of our self-adhesive labels with perforation: 50x30 mm. , 56x32 mm. , 70x25 mm. , 70x190 mm. , 70x208 mm. , 82x140 mm. , 90x48 mm. , 100x50 mm. , 100x160 mm. , 102x102 mm. , 102x152, 5 mm. , 102x48 mm. , 102x150 mm. , 105x74 mm. , 105x149 mm. , 111x73 mm. , 150x208 mm. , 166x74 mm.
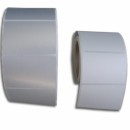
Also called metallized aluminum films, belong to a group of specialised labels. They are used for marking metal products. Material of aluminum foils are odorless, nontoxic, completely opaque and resistant to most solvents, oils, fats, waxes, gas and foodstuffs. These labels are also resistant to very high temperatures, moisture, UV rays, dirt, dust, chemical agents, tearing, and water. They provide identification of the products even after many years of use.
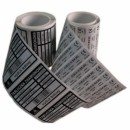
"Plates" may also serve as a "warranty seal".
Name plates are intended for marking assets records of entities and for printed circuit boards and on different surfaces. Surface material for the name plates that are used would be plastic films (polyester), metal, frosted and / or glossy, polypropylene (high temperature). On rating plate acrylic adhesives, durable and unsurpassed with increased thickness suitable for bonding to the dusty, rough, even greasy surfaces are used. If "diagrams" are glued directly onto electronic components labels that do not conduct electricity and does not accumulate static electricity is advisable.
"Plates" are printed on special plastic labels, which are characterized by high long-term durability and good adhesion to the substrate. Mechanical factors such as labels printed with additional collateral in the form of transparent security label or laminated , can increase the durability and resistance.
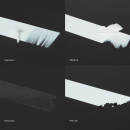
The principal feature of security labels and what characterizes them most is that such labels can not be re-glued to the protected goods without notice of tampering. Security Labels (warranty seal) can be grouped into two types. Self-adhesive labels provided with a layer of security properties, which layers are destroyed due to breaking up. This characteristic stratification of the label makes it impossible to re-glue it.
The first type is a plastic label, which when you try to peel-off disintegrates. For this purpose special labels made of white plastic "polyethylene" (PE) on the surface of paper or white "polyvinyl chloride" (PVC) are used. This kind of plastic labels are mainly used as a replacement guarantee seal and all kinds of vignettes confirming the fee for the use of the highway. Label crushing is used as a permanent marker (products, devices, components), whose labels cannot be re-used. These labels have a very strong adhesive in relation to the structure of the material of the label. Such labels crumble when you try to break it into small pieces, or stretch, which prevents their separation in its entirety.
The second type of labels is one that leaves lasting traces of adhesive or as a string. It is made of a plastic film, which remains after the breach in the outer shell disclosing a durable string. Part of the shell of the film is transferred to the protected material by giving the words, while the film is formed lasting lettering transparent. On the surface there are inscriptions: VOID, OPENED, TAMPERED. Frequently these labels are made of metalized "polyester film" (PET).
Sealing labels are intended to protect the finished product during the warranty period. Breaking the seal will void the warranty. Labels can be glued on flat and slightly curved, and joints of different elements. It is generally used in the electronics and computer industry and to protect perfume, cosmetics, documents and packages. Destruction of the security label indicates tampering to the device or packaging. While the equipment is under warranty, the seal may not be broken.

Transparent labels for cosmetics perfumes shampoos. Made of transparent PP (polypropylene) or PE (polyethylene). The main task of transparent labels is their appearance - aesthetics. These are the labels for customers requiring the most from the appearance of their product. For these labels, price is not as important as quality labels.
When you print bar codes on labels with transparent film, remember that the best solution is white Overlay under the bar code. With this solution we get a better readability of the barcode. Otherwise, the contrast between the text and the color code packaging may be so small that the reader did not pick up the codes.
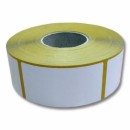
VINYL Labels. They are made of a special material VINYL with a super strong adhesive. The most popular dimensions are 100x80 mm.
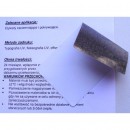
What to do when we want to cover something with a label? The solution is COVER labels that cover. OPAQUE labels are opaque, non-transparent. They are also called covering labels. These labels have a black/gray/blue/pink color on the adhesive side. The most commonly used top material is white glossy uncoated paper but unfortunately paper is not resistant to weather conditions and in such cases we use OPAQUE films. Due to the higher price, PE polyethylene film is rarely used as a covering label and PP polypropylene film is more often used. Customers require adhesive with very good cohesion and initial adhesion so that it is difficult to peel off from the surface. There are no biodegradable films. COVER labels are supposed to cover various surfaces and therefore samples should be tested. The most difficult materials to cover are cardboard boxes because their composition or the varnish they are coated with is unknown, they may contain substances (plasticizers or silicones) that make it difficult to stick them, they may cause deactivation of the adhesive over time.
In the picture, the first example of a standard paper label. As you can see, it is transparent, with the inscription CISOWIANKA perlage on the bottle. Foil labels that do not shine through in order from cheapest to most expensive:
-
Black PP opaque foil label printed on the back,
-
Blue PP opaque foil label printed on the back,
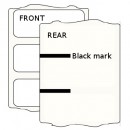
Labels with a black marker on a silicone backing.
Labels with a black marker on a silicone substrate. The black mark is printed by a flexographic machine printing on non-adhesive and self-adhesive labels. The print is usually made on the reverse side of the label or on the silicone substrate. Some labels do not have a side cut or spacing between labels that are specifically used to recognize subsequent labels by the printer. Transparent film labels often cause problems. The label printer’s photocell cannot recognize the material’s transparency because the material is 100% transparent. The label printer’s photocell recognizes transparencies and gets lost when the top material is transparent. The solution to this problem is to print a black mark - MARKER. The downside of this solution is the higher cost of the label because it contains additional prints. Transparent biodegradable films made of cellulose have also appeared on the market. The black strip is printed across the width of the silicone substrate tape, and its height is almost always equal to the spacing between labels. The height of the strip varies depending on the die used on a given roll.
Black marks are rarely used for paper labels when the printer has an unusual system for recognizing spacing between labels, when it has an unusual shape or is round and the printer does not have a movable sensor for subsequent labels. For film labels, especially transparent ones, white glassine 65 silicone substrates with a thickness of 55 microns or high density 70 wh with a thickness of 56 microns are recommended, i.e., white substrates rather than honey or yellow ones. They are well suited for photocell-assisted labeling systems because they print well and create good contrast. White Kraft substrate is not suitable for film labels with black markers as it prints poorly and is more difficult.